Renovation Town Hall
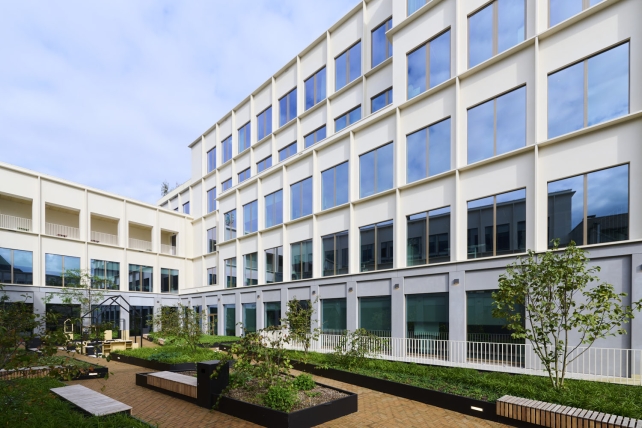
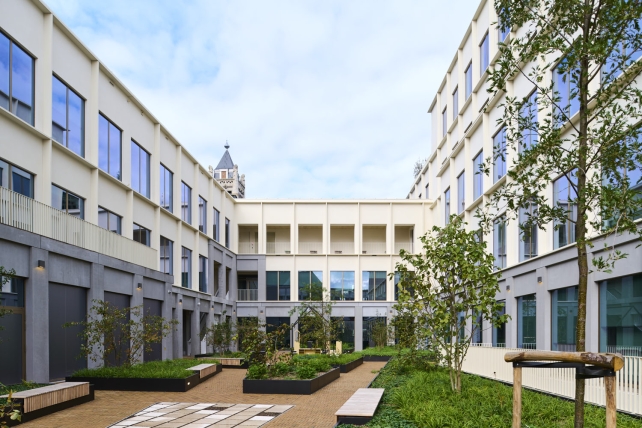
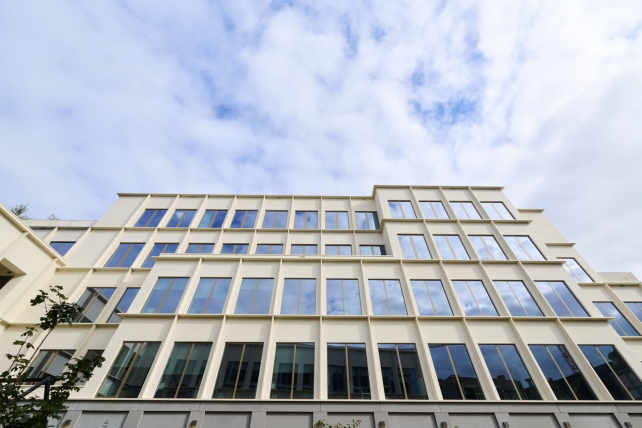

This project was carried out by
Luckx • Rue Robert Gérard 3 • 1480 Tubeke
02/ 363 00 90
info@luckx.be
https://www.luckx.be/
Custom-made aluminium profiles for renovation of Town Hall
The city of Roeselare has given its town hall a thorough facelift. Much attention was paid to circularity and energy efficiency. A new building was also attached to the historic building, a progressive complex with a sleek interplay of vertical and horizontal aluminium fins, custom-made by Aliplast Aluminium Systems.
The city council launched in 2019 a procedure to renovate and upgrade the City Hall. Not only the historical part was renovated, but the buildings without heritage value made way for a contemporary new building to house the administrative services. Within the u-shaped building, a public garden was created to give Roeselare's city centre a green impulse.
Building according to ecological principles with respect for budget
B-architects and Bressers Erfgoed designed this beautiful project with a maximum focus on circular construction such as reuse, flexibility and disassembly. Other important factors are sustainability and ecology, such as climatisation with residual heat from the local incinerator.
‘It was a challenging exercise to find an ideal balance between the design envisaged by the architects, the needs of the city council and the available budget,’ Frederic De Reu, project manager of coordinating contractor Maes, explains. ‘It was in fact initially planned that the cladding would be realised in architectural concrete, but due to sudden price increases this no longer fitted within the budget. Therefore, only the underside of the façade was done in architectural concrete. We wanted to finish the rest of the façade with crepi, but in that case we had to look for a solution to realise the tight mix of horizontal and vertical lines. For that, we contacted Luckx, installer of the exterior joinery on this project.
Technical masterpiece
Luckx proposed a solution using Aliplast systems. Given the emphasis on sustainability - in line with BREEAM Excellent guidelines - Aliplast Aluminium Systems was an obvious choice as supplier of the exterior joinery: the Star 75 windows in this project have Cradle to Cradle Silver certification.
In order to respect the interplay of lines in a budget-conscious way, without sacrificing construction-technical quality, it was decided to use vertical and horizontal aluminium fins, custom extruded by Aliplast. Jens Plantefève-Castryck, director at Luckx: ‘Aliplast has excellent expertise in profile development. The architectural fins, initially conceived in precast concrete, were replaced by aluminium extrusion profiles tailored to this project: with attention to stability, waterproofing and long-term durability. All in a cost-effective manner.’
‘Thanks to the excellent support from Luckx and Aliplast, we were able to fine-tune all the technical details, the execution went off peak and we were able to perfectly match the crepi cladding to the windows and fins,’ adds Frederic De Reu. ‘The final result may look simple, but a lot of thought and optimisation went into it. ’
A challenging eye-opener
Els Uvyn, project manager at Aliplast, agrees: ‘It was a challenging engineering exercise where we had to be very short on time, given the tight timing. We were able to respect this as we develop and produce everything in-house.
To arrive at a suitable solution quickly, we set up a team that checked everything immediately with the parties involved: not only in terms of design, but also in terms of stability, waterproofing, practical feasibility, etc. In the end, we proposed a combination of vertical fins between the windows and a continuous horizontal fin above each floor. We developed a custom-made mould for this: we used it to extrude the necessary profiles on our own presses. We also custom-made all anchors used to attach the fins to the underlying structural shell. These anchors were subjected to additional calculations in collaboration with a specialised engineering firm, as the impact of wind and deformation had to be correctly mapped there as well.
It is a brilliant project in which we once again pushed boundaries. No doubt an eye-opener for many designers that they can use aluminium so ‘out of the box’.’
Custom-made aluminium profiles for renovation of Town Hall
The city of Roeselare has given its town hall a thorough facelift. Much attention was paid to circularity and energy efficiency. A new building was also attached to the historic building, a progressive complex with a sleek interplay of vertical and horizontal aluminium fins, custom-made by Aliplast Aluminium Systems.
The city council launched in 2019 a procedure to renovate and upgrade the City Hall. Not only the historical part was renovated, but the buildings without heritage value made way for a contemporary new building to house the administrative services. Within the u-shaped building, a public garden was created to give Roeselare's city centre a green impulse.
Building according to ecological principles with respect for budget
B-architects and Bressers Erfgoed designed this beautiful project with a maximum focus on circular construction such as reuse, flexibility and disassembly. Other important factors are sustainability and ecology, such as climatisation with residual heat from the local incinerator.
‘It was a challenging exercise to find an ideal balance between the design envisaged by the architects, the needs of the city council and the available budget,’ Frederic De Reu, project manager of coordinating contractor Maes, explains. ‘It was in fact initially planned that the cladding would be realised in architectural concrete, but due to sudden price increases this no longer fitted within the budget. Therefore, only the underside of the façade was done in architectural concrete. We wanted to finish the rest of the façade with crepi, but in that case we had to look for a solution to realise the tight mix of horizontal and vertical lines. For that, we contacted Luckx, installer of the exterior joinery on this project.
Technical masterpiece
Luckx proposed a solution using Aliplast systems. Given the emphasis on sustainability - in line with BREEAM Excellent guidelines - Aliplast Aluminium Systems was an obvious choice as supplier of the exterior joinery: the Star 75 windows in this project have Cradle to Cradle Silver certification.
In order to respect the interplay of lines in a budget-conscious way, without sacrificing construction-technical quality, it was decided to use vertical and horizontal aluminium fins, custom extruded by Aliplast. Jens Plantefève-Castryck, director at Luckx: ‘Aliplast has excellent expertise in profile development. The architectural fins, initially conceived in precast concrete, were replaced by aluminium extrusion profiles tailored to this project: with attention to stability, waterproofing and long-term durability. All in a cost-effective manner.’
‘Thanks to the excellent support from Luckx and Aliplast, we were able to fine-tune all the technical details, the execution went off peak and we were able to perfectly match the crepi cladding to the windows and fins,’ adds Frederic De Reu. ‘The final result may look simple, but a lot of thought and optimisation went into it. ’
A challenging eye-opener
Els Uvyn, project manager at Aliplast, agrees: ‘It was a challenging engineering exercise where we had to be very short on time, given the tight timing. We were able to respect this as we develop and produce everything in-house.
To arrive at a suitable solution quickly, we set up a team that checked everything immediately with the parties involved: not only in terms of design, but also in terms of stability, waterproofing, practical feasibility, etc. In the end, we proposed a combination of vertical fins between the windows and a continuous horizontal fin above each floor. We developed a custom-made mould for this: we used it to extrude the necessary profiles on our own presses. We also custom-made all anchors used to attach the fins to the underlying structural shell. These anchors were subjected to additional calculations in collaboration with a specialised engineering firm, as the impact of wind and deformation had to be correctly mapped there as well.
It is a brilliant project in which we once again pushed boundaries. No doubt an eye-opener for many designers that they can use aluminium so ‘out of the box’.’
Products used
Commercial brochures
This project was carried out by
Luckx • Rue Robert Gérard 3 • 1480 Tubeke
02/ 363 00 90
info@luckx.be
https://www.luckx.be/